EXPLORE THE CAPABILITIES
GET STARTED TODAYOur engineering expertise and state-of-the-art equipment are perfectly aligned to meet cost, quality, and delivery goals for stamped metal parts. Progressive stamping is usually the best alternative when repeatability, tight tolerances, and large quantities are required. Our stamping possibilities include components used in the following industries:

PROGRESSIVE STAMPING EXPLAINED
In progressive stamping, a continuous metal coil is fed through a series of die stations, and one or more operations are performed simultaneously and sequentially at each station and then automatically advanced to the next station with each stroke of the press. Each step is built on the previous step until the desired shape is attained. The parts are held in a strip until they have completed all the steps, including forming, punching, shaping, bending, cutting, shaving, extruding, drawing, embossing, hemming, coining, and piercing. Once all steps are completed, the part is cut from the strip. Progressive die stamping saves time by performing several operations concurrently, but the tooling is typically more expensive. Stamping is a low-cost and high-speed manufacturing process of making large quantities of metal parts. From simple to elaborate, we deliver exceptional products at an affordable price.
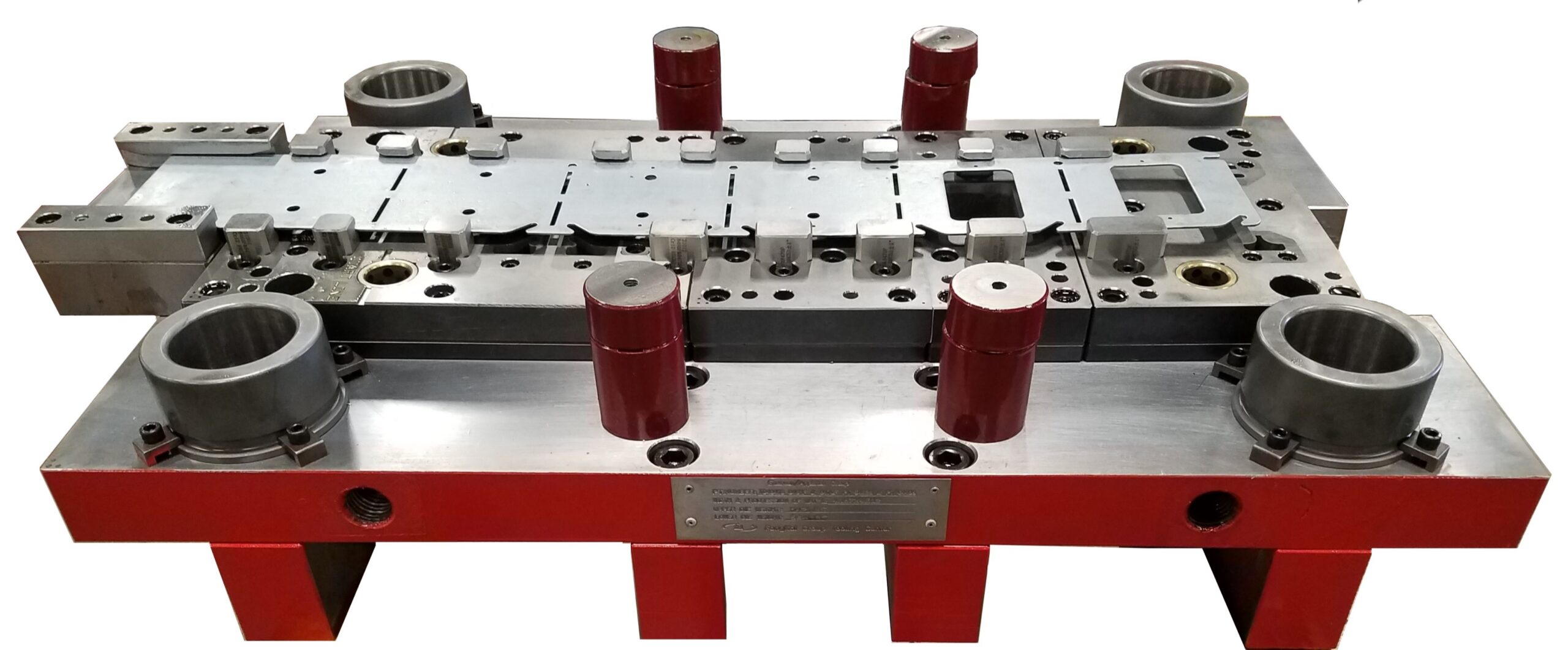
STAMPING PRESSES WORLDWIDE
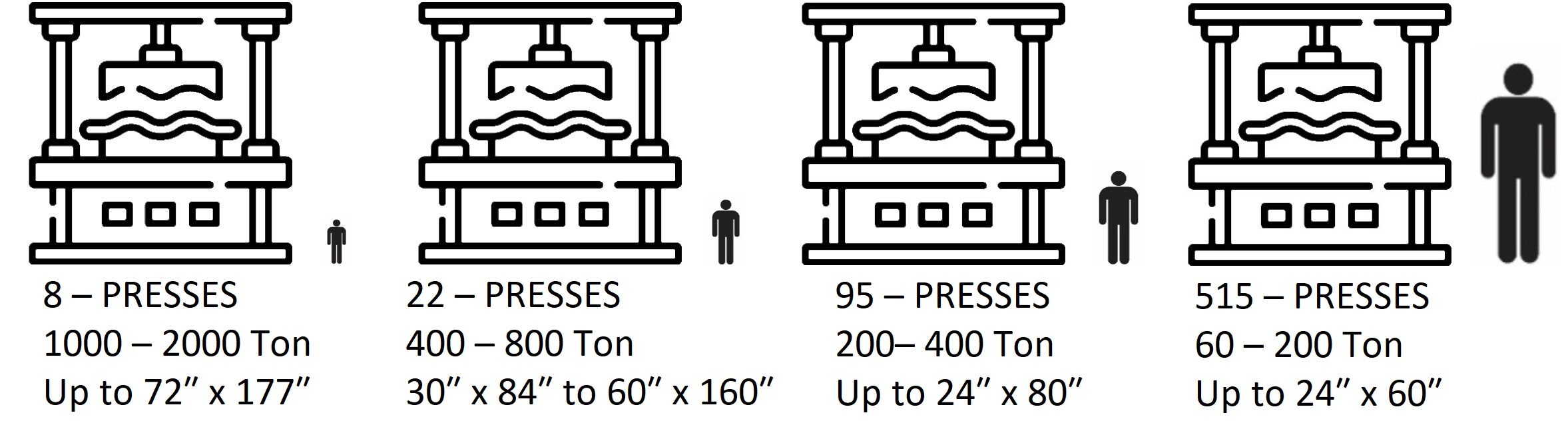
CAPABILITIES
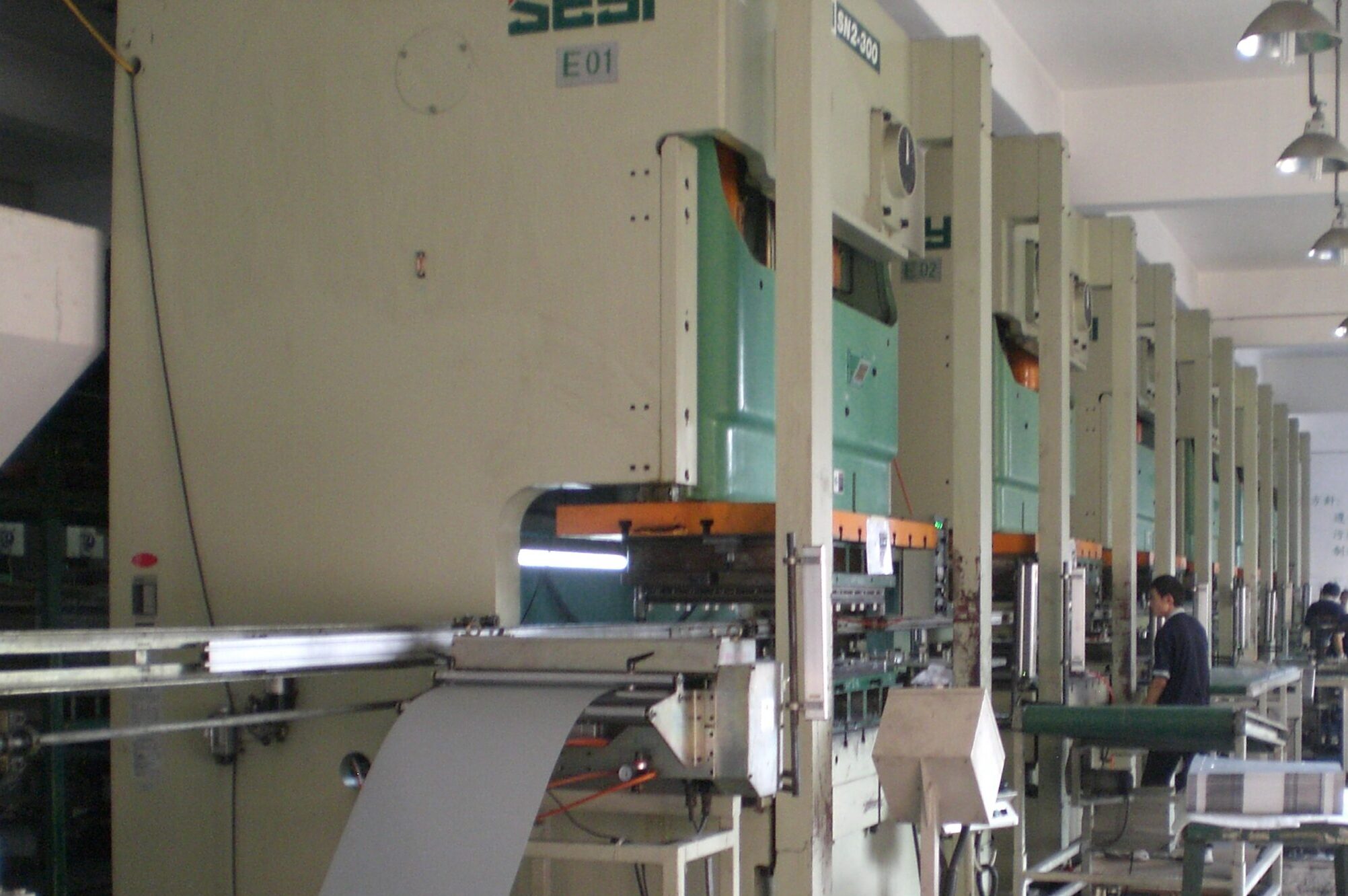
WORLDWIDE PRODUCTION
• Over 620 metal stamping presses
• 60 Ton up to 2000 Ton
• Presses Beds up to 72″ x 177″
• Progressive & Transfer Stamping
• Class-A-Cosmetic products
• Specializing in Deep Draw stamping of larger components
• In-House Tooling Build & Maintenance
• Extensive use of sensor technology to protect tooling during production
• Detailed quality inspections completed on the shop floor and the quality lab.
• US Qualifications available to reduce overseas travel of Engineering Resources
• World-class manufacturing from multiple locations overseas or from our US facility
• All stamping facilities are certified (ISO 9001) in 2015 or better.
ADDITIONAL SERVICES INCLUDE:
• Assembly
• Hardware Insertion
• Laser Welding
• Pre-Plating or Post-Plating
• Powder Coat, Wet Paint, or E-Coating
• Passivation
• Welding
• Tapping
• Deburring
• Heat Treating
• Printing
• Over-Coating
DOMESTIC OR OVERSEAS QUALIFICATIONS
With our Texas stamping and tool & die facilities, FKI will reduce engineering budgets while improving productivity. We commonly support ECN/ECR requests locally before PPAP and during product life. The strategy of approving part geometry in our overseas facilities before shipment, with final buy-off and approval in Texas, is very beneficial to our North American clients.
DESIGNING A METAL PART
When designing a stamped metal component, several key factors must be considered, including unique product requirements, material selection, durability, die design, part size, and the ability to produce for mass production effectively. Our Engineering staff can assist you in designing the best possible solutions within your budget. FKI can suggest the proper tooling requirements and maximize results.
DFM SIMULATION
Computer simulations are used to perform DFM on all parts before manufacturing. The design’s digital testing can improve the final part’s time, costs, and physical testing.
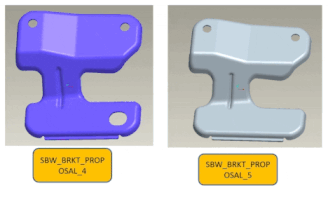
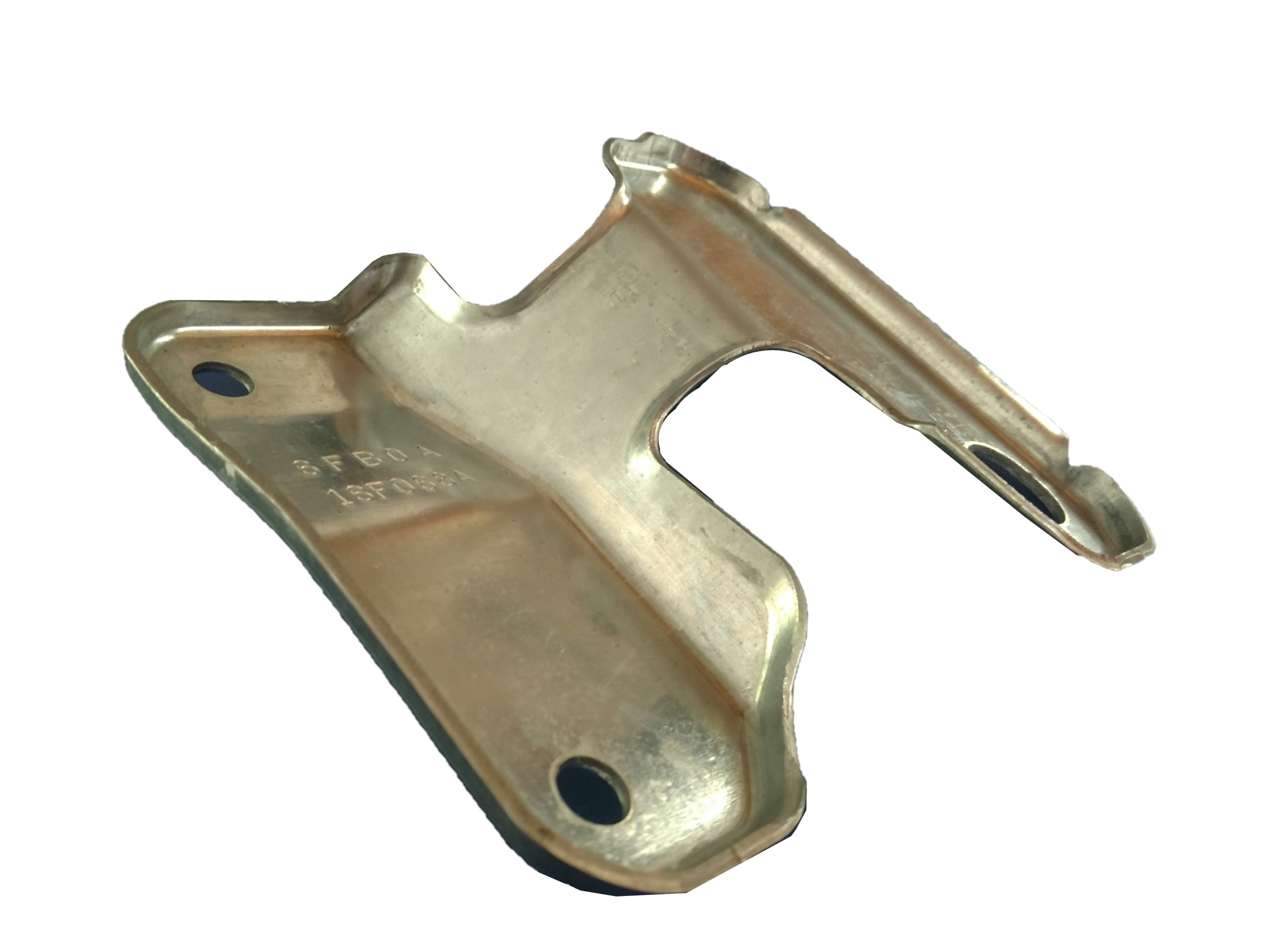
CLASS A COSMETIC
FKI’s specialty is manufacturing high-volume cosmetic Class A decorative products that are difficult for other manufacturers to produce. FKI also provides component assembly to improve production and reduce manufacturing lead time.
SUPPORTING DEVELOPMENTS
• Complete Turnkey Project Management
• FKI can handle large Tooling Packages from multiple suppliers/customers
• Virtual Design Review
• PPAP- US Qualifications Available to Reduce Overseas Travel of Engineering Resources
• Test Fixture and Jig Development in Accredited Certified Facilities
• Simulation Validation and Reporting
• Laser Welded Fabrication
• Weldments and Assemblies
KEY BENEFITS
• High Volume
• Repeatability
• Increased Speed
• Reduced Scrap
• Difficult Geometrics
• Quick Setup
• Low Cost Per Part
• US & Overseas Engineering and support
• Low maintenance tooling
• Recyclable
OEM PRODUCTS
Doors, Sinks, Skins, Panels, Liners, Cook Tops, Housings, Burner Bowls, Frames, Sinks, Pans, Covers, Lids, Trim, Brackets & Bases, Basins, Tanks, Trays, Wells, Chambers, Canisters, Containers, Shields, Enclosures, Reservoirs, and Basins. Interior Trim, Seating, Brackets, Housings, Pans, Covers, Bezels, Door Handles, and Panels
THICK, THIN, BRIGHT, SATIN & MILL FINISH
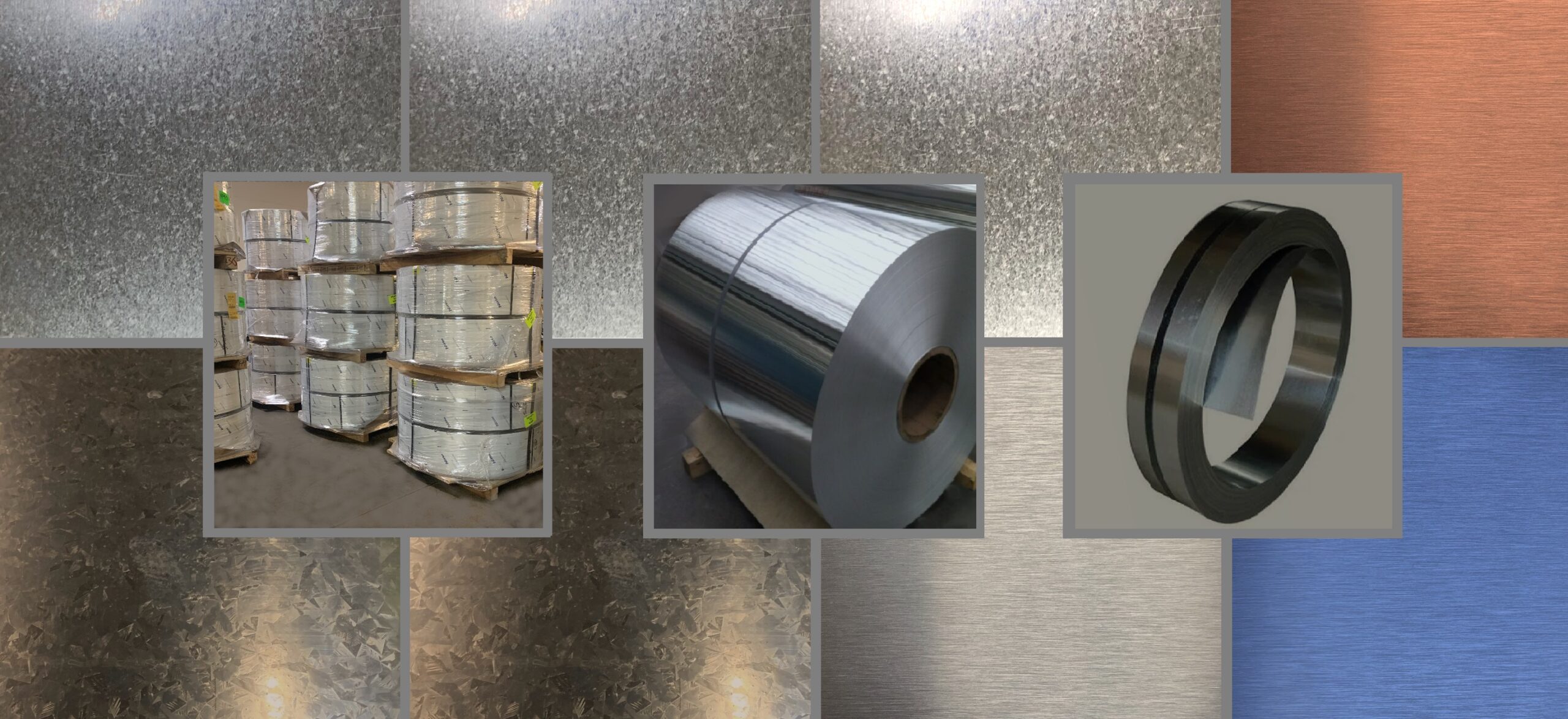
We offer metals ranging from .012” to .500” in thickness.
MATERIALS
• Stainless Steel
• Aluminum
• Cold Rolled Steel
• Pre-coated Steel & Aluminum
• Electro-Galvanized
• Aluminized Steel
• Enameled Steels
• Bright, Brushed, or Mill Finish
• High Strength Low Alloy Material
HOW IT’S MADE
“When repeatability and large quantities are required, then stamping is usually the best alternative.”
WATCH VIDEO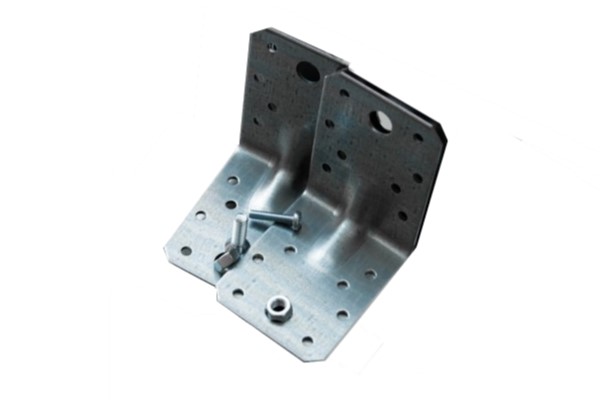
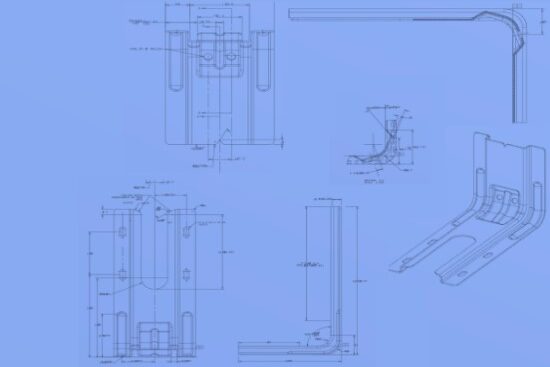
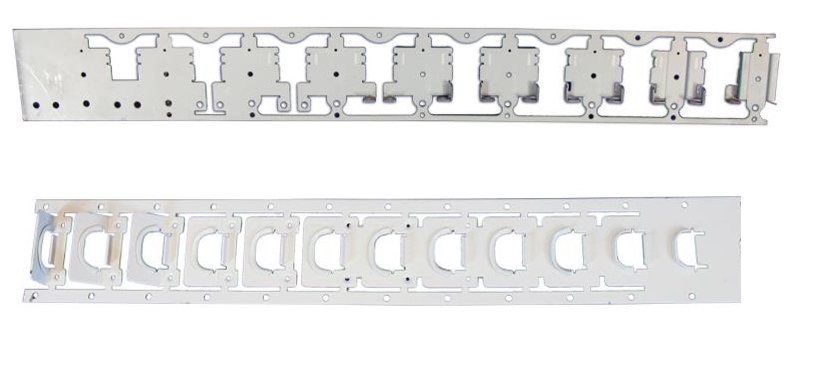
THE FKI ADVANTAGE
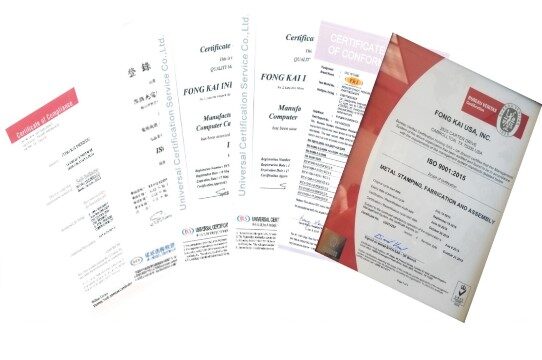
QUALITY &
CERTIFICATIONS
LEARN MORE 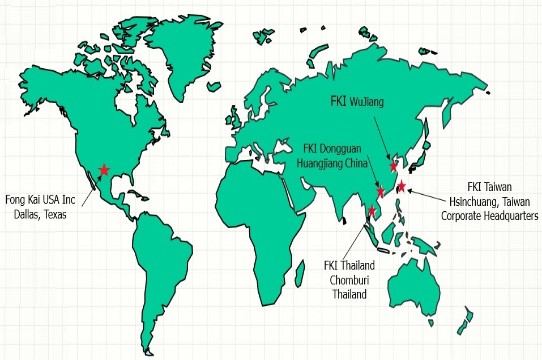
GLOBAL LOGISTICS &
PLANNING
LEARN MORE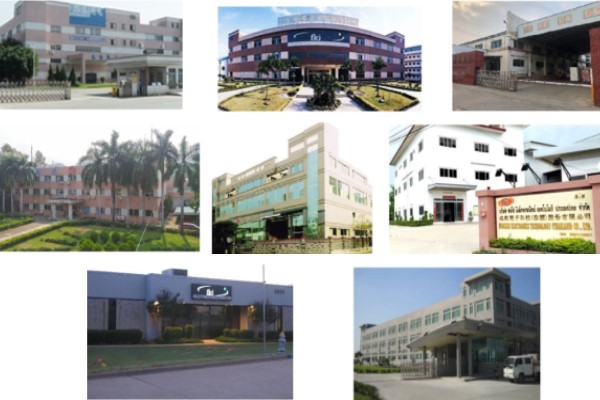