EXPLORE THE CAPABILITIES
GET STARTED TODAYFKI has the expertise and engineering capabilities to meet customers’ expectations on complex products and deep-drawn parts commonly used in industrial applications. We handle all phases, including product design, tooling design, manufacturing, metal stamping, plastic injection molding, finishing, part assembly, packaging, part decoration, and logistics. Working with us gets you results, ultimately less costs, more value, and less risk. FKI is recognized worldwide as an expert in stamping industrial components for Fortune 1000 customers. Our team is positioned to support both high-volume and complex components for Industrial products, including but not limited to:
METAL COMPONENTS
Metals improve the product’s aesthetic appeal and align with your branding. Metal offers both durability and strength and can resist rust, fire, heat, wear, and corrosion. Metals also have high thermal and electrical conductivity and can withstand high temperatures and frequent use. We will help you produce a cost-effective, high-quality part that meets or exceeds your needs.
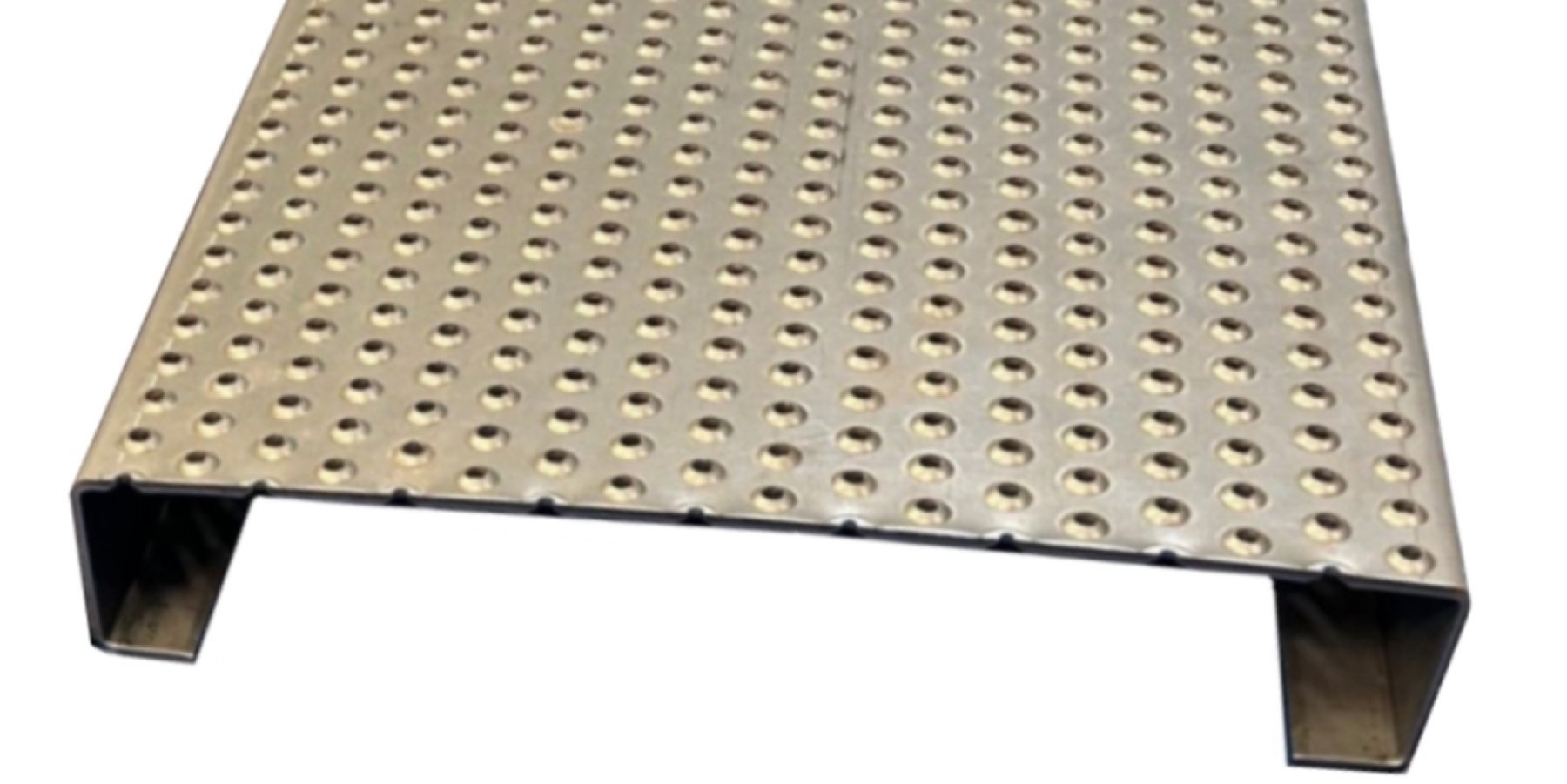
CAPABILITIES
• Over 620 metal stamping presses worldwide.
• 60 Ton up to 2000 Ton
• Presses Beds up to 72″ x 177″
• Progressive & Transfer Stamping
• Class A Cosmetic products
• Specializing in Deep Draw stamping of larger components
• In-House Tooling Build & Maintenance
• US Qualifications available to reduce overseas travel of Engineering Resources
• World-class manufacturing from multiple locations overseas or from our US facility
• All stamping facilities are certified (ISO 9001) in 2015 or better.
ADDITIONAL SERVICES INCLUDE:
• Assembly, Wet and Dry Coatings, Printing, Tapping, Coating, Deburring, Plating, and PVD Coating
MATERIALS
• Stainless Steel
• Aluminum
• Cold Rolled Steel
• Pre-coated Steel & Aluminum
• Electro-Galvanized
• Aluminized Steel
• Enameled Steels
• Bright, Brushed, or Mill Finish
• High Strength Low Alloy Material
DESIGNING A METAL PART
When designing a stamped metal component, several key factors must be considered, including metal selection, durability, die design, part size, and the ability to mass produce effectively. Our Engineers help you design the best possible solution for stamping needs and can suggest working with progressive tooling or hand transfer tools, depending on your requirements.
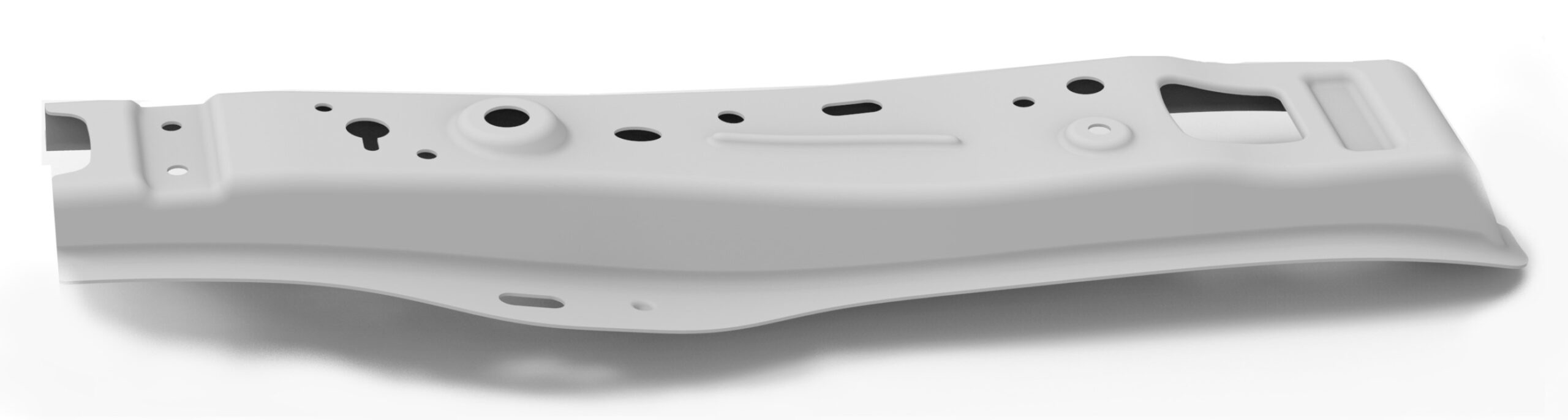
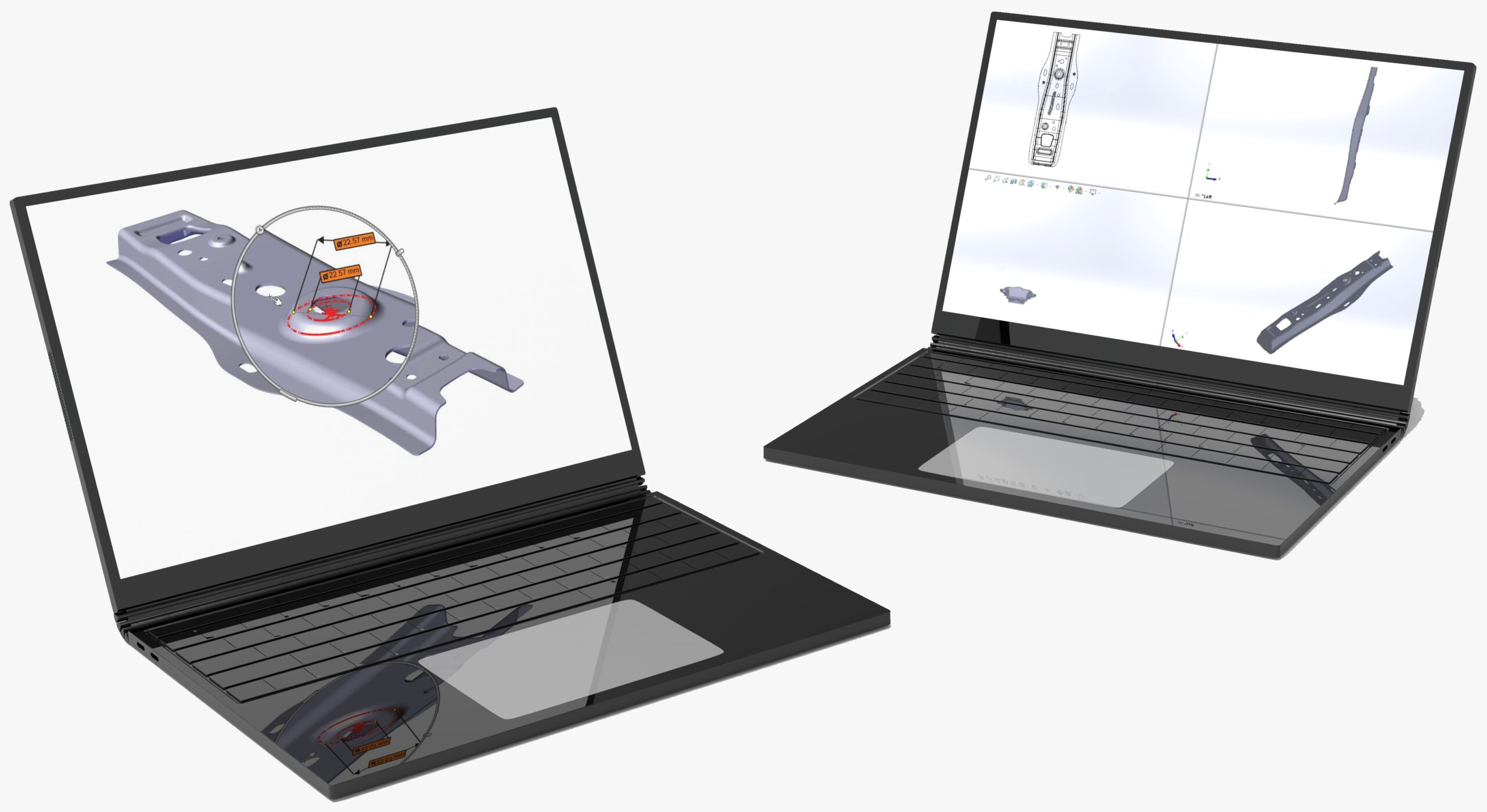
PLASTIC COMPONENTS
Plastics are used in various Industrial/OEM applications to improve durability, visual appeal, and affordability. These plastic components are crucial for the appliance industry because they offer many advantages over other materials. Plastics are lightweight, customizable, and enhance product performance.
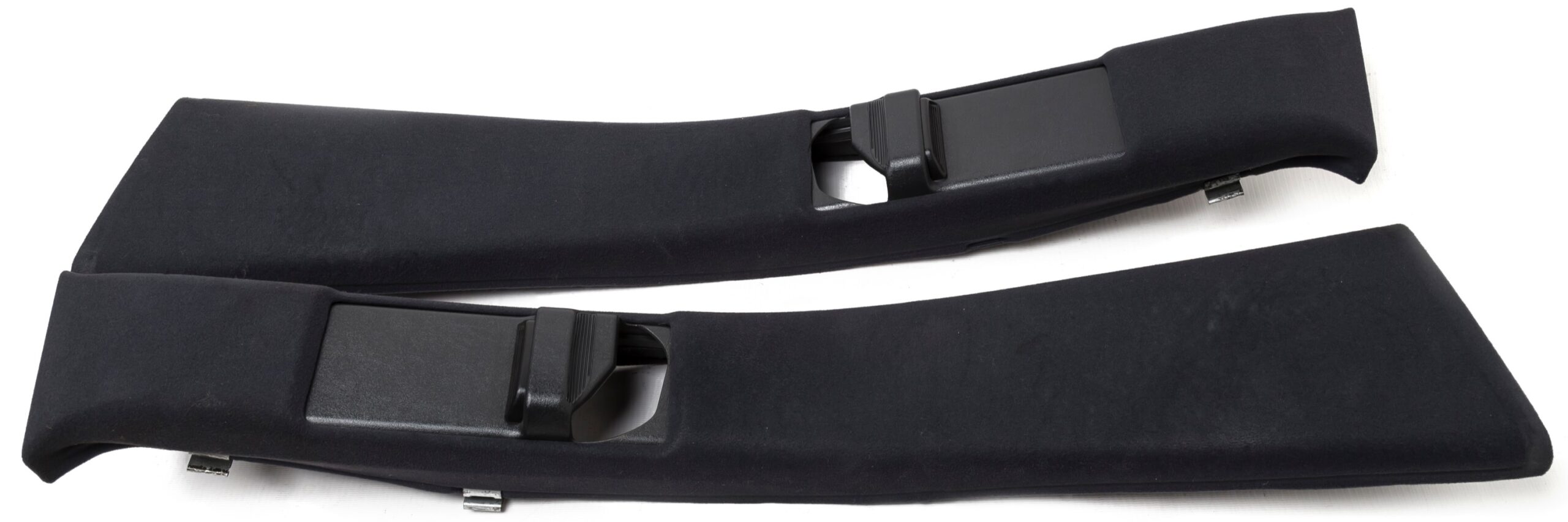
CAPABILITIES
• 400 plus injection molding machines worldwide
• Presses up to 1600 tons
• Sizes up to 85″ LCD Screens and 5KG shots possible
• Class A Cosmetic finishes
• Specializing in High Cosmetic finishes on larger components
• Pad Printing and Silk Screen Processing
• In-House Tooling fabrication & Maintenance
• Overseas Qualifications available
• World-class manufacturing from multiple locations overseas
• All our injection molding facilities are certified (ISO 9001) 2015
ADDITIONAL FEATURES INCLUDE, BUT NOT LIMITED TO:
Paint Wet and Dry application, Multi Material Multi Shot, Plating and CNC Machining
MATERIALS
• ABS – Acrylonitrile Butadiene Styrene
• PE – Polyethylene
• PC – Polycarbonates
• HIPPS – High Impact Polystyrene
• PET – Polystyrene
• PP – Polypropylene
• Nylon
• Proprietary Polymers
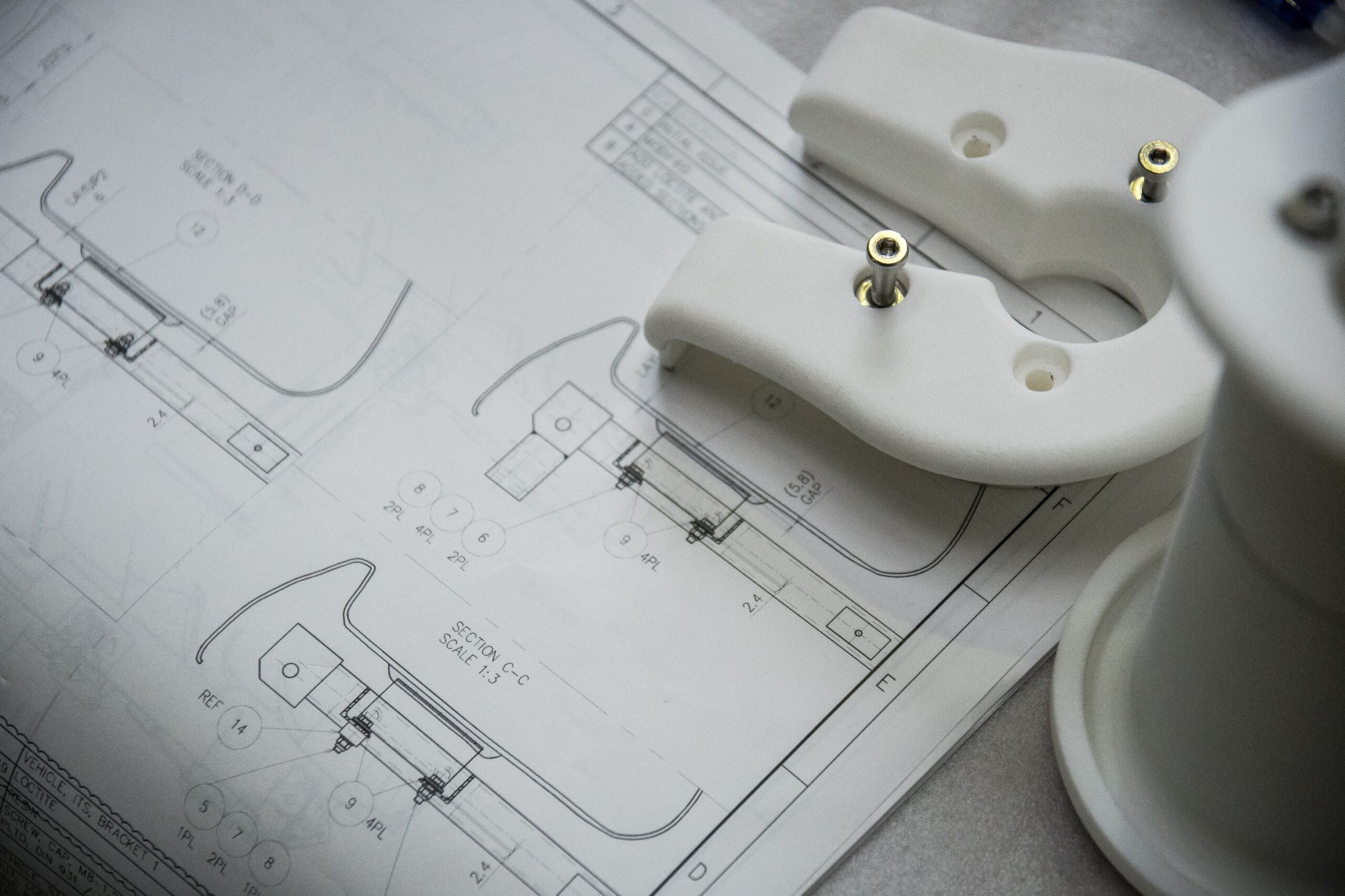
DESIGNING A PLASTIC PART
Designing a plastic component requires careful consideration of many factors, including molding, part area, material selection, and mass production. We can offer injection molding, blow molding, or thermoforming, and our engineers can help design a quality part. We assist you in choosing the proper material and can consider factors like heat resistance, durability, and strength. Most importantly, our staff can help ensure the part can be manufactured effectively in mass quantity at a reasonable price.
TOOLING TRYOUT – OVERSEAS OR DOMESTIC
All 5 of our stamping plants and four injection molding plants have extensive in-house tooling capabilities. With our Texas stamping and tool & die facilities, FKI will reduce engineering budgets while improving productivity. We commonly support ECN/ECR requests locally before PPAP and during product life. The strategy of approving part geometry in our overseas facilities before shipment, with final buy-off and approval in Texas, is very beneficial to our North American clients.
WATCH VIDEO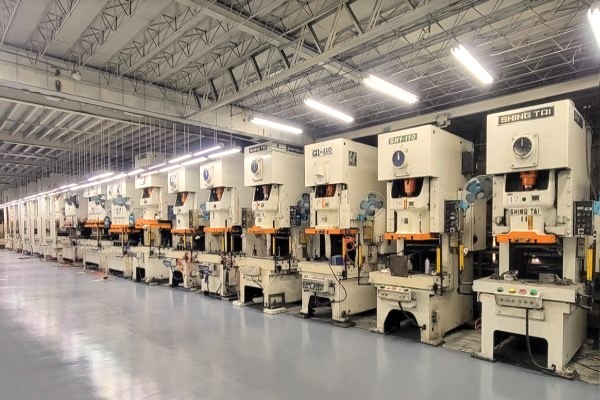
THE FKI ADVANTAGE
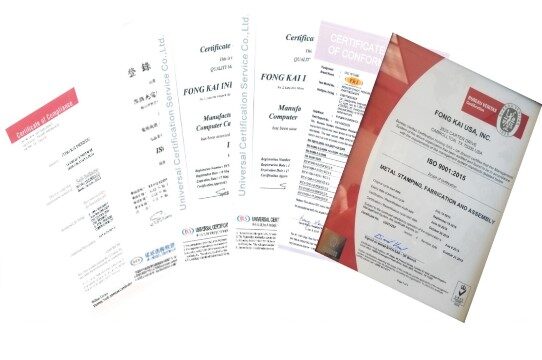
QUALITY &
CERTIFICATIONS
LEARN MORE 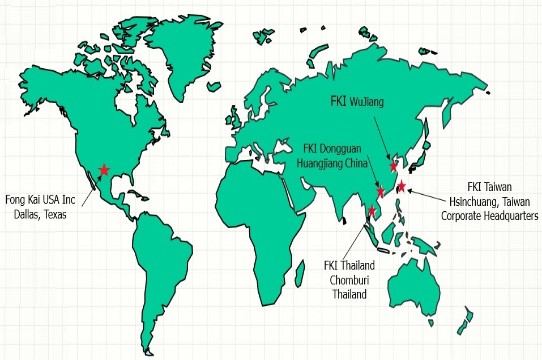
GLOBAL LOGISTICS &
PLANNING
LEARN MORE 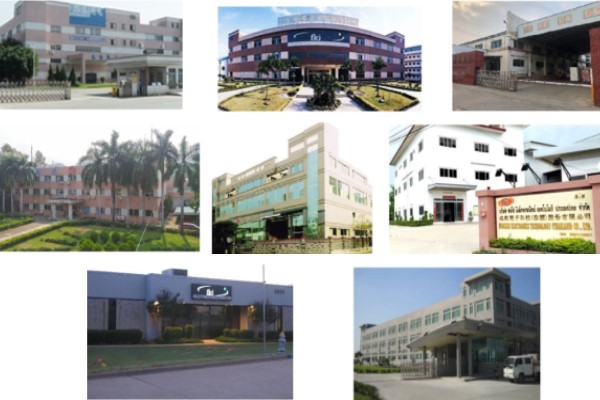