EXPLORE THE CAPABILITIES
GET STARTED TODAYBrake Press converts a flat sheet of metal or workpiece into a formed part using a V or U-shaped concave opening. A wedge-shaped tool or knife applies force onto the workpiece, pushing it into the metal into the V or U-shaped opening, causing the metal to bend to the chosen angle. Bending typically does not change the material thickness, and CNC controls adjust the position, depth, and force applied to the workpiece. We make products for the following industries.

HYBRID FORMED PARTS
Below is an example of one of our more complex appliance parts manufactured using a laser to cut the blanks, a stamping press to add details, and a press brake to accomplish the final bends. Very few companies can achieve these results, as they lack the proper equipment. Fiber Laser Cutting blended with secondary “Big Stamping” has become an essential part of the metal fabrication process and a significant advantage when working with FKI. The precision of the laser allows for either short or long-run parts to be created without the need for costly tooling and longer lead times. Our large bed stamping presses enable us to make complex forms or subassemblies that can’t be done on a press brake or economically made on a turret. This process is ideal for complex parts with short product life cycles and JIT production.
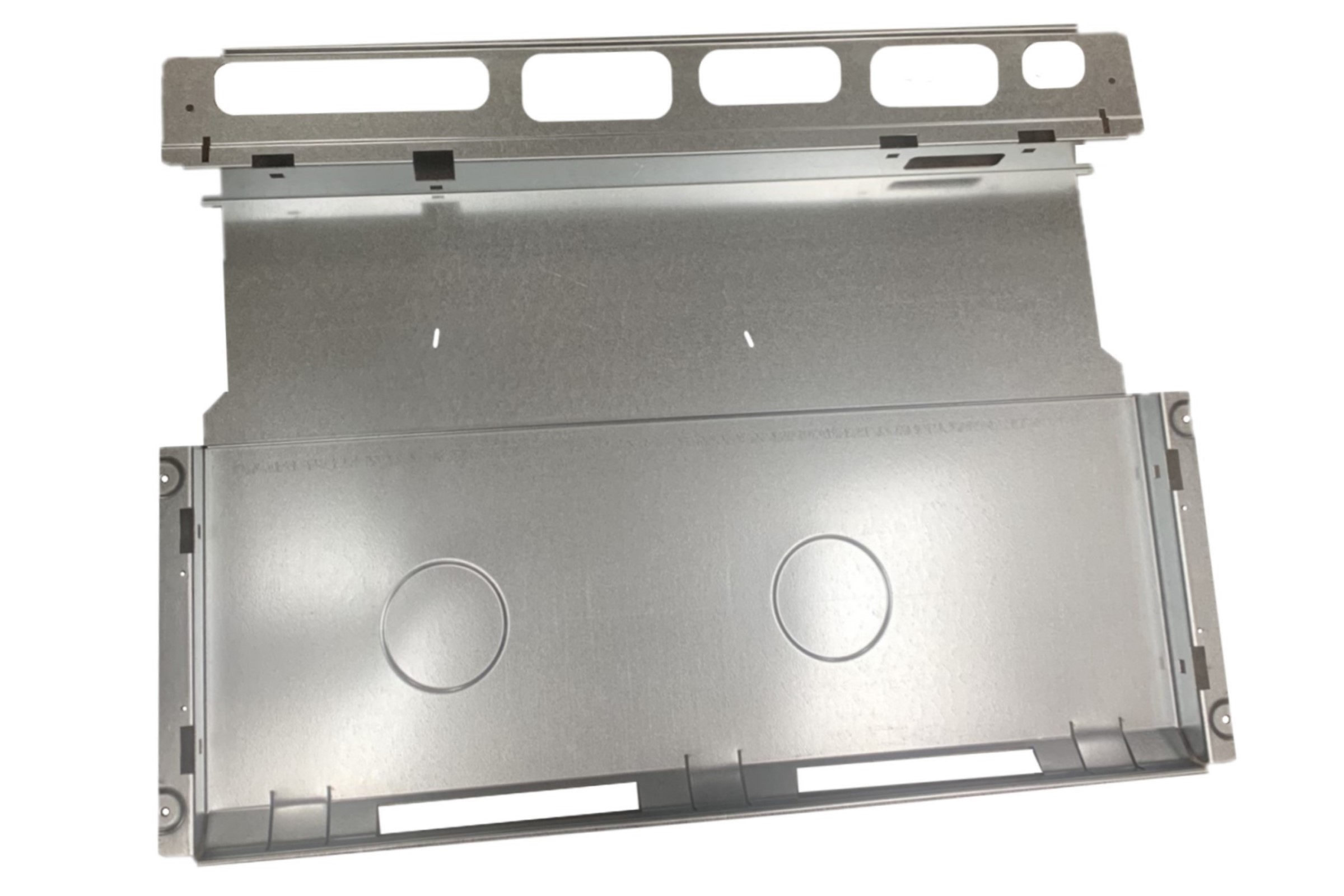
ADVANTAGES
• In-house tooling and machining capabilities.
• Ideal for smaller volume production
• Highly accurate, but not as accurate as stamping
• Flexibility in adjusting tools & dies
• Speed
TYPES OF BENDS
V-BENDING
This method uses a v-shaped die and punches to bend sheet metal to achieve acute, obtuse, or 90° bend angles.
AIR BENDING
This leaves space (or air) underneath the sheet, allowing for more bend angle control than conventional V-bending. The result is higher accuracy due to less spring-back.
BOTTOM BENDING
This method requires a higher tonnage press to achieve precise bend angle control.
WIPE BENDING
It involves holding the sheet metal against a wipe die via a pressure pad and using a punch to force the edge of the sheet beyond the die and pressure pad, causing it to bend.
ROLL BENDING
Uses sets of rollers to feed (and bend) the metal stock into rolls, tubes, cones, or curved shapes.
ROTARY DRAW BENDING
The sheet metal is clamped to a rotating die and drawn around the die to form a geometry that matches the desired bend radius, with an internal supporting mandrel to prevent wrinkling on the surface and minimize the risk of scratches.
CAPABILITIES
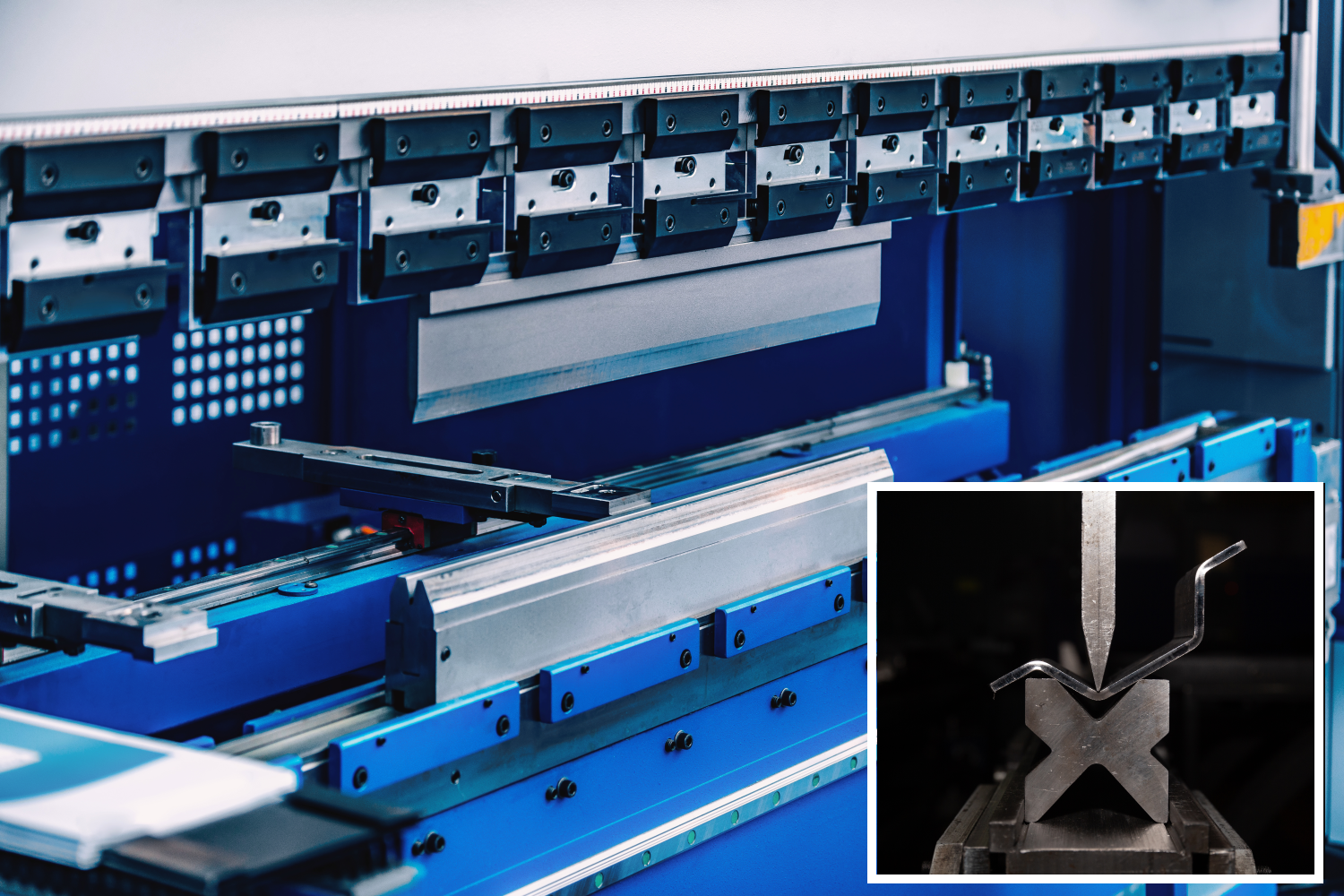
• Precision bending up to 18 ft.
• Multiple press brakes up to 440 tons
• Carbon Steel, Stainless & Aluminum
• Typically, no extended lead time or costly tooling
• Quick turn prototypes
• Cost-effective manufacturing.
• PVC masking.
THICK, THIN, BRIGHT, SATIN & MILL FINISH
FKI is an experienced metal stamping manufacture that can develop simple to complex products using an assortment of metals ranging from .012” to .500” in thickness.
MATERIALS
• Stainless Steel
• Aluminum
• Cold Rolled Steel
• Pre-coated Steel & Aluminum
• Electro-Galvanized
• Aluminized Steel
• Enameled Steels
• Bright, Brushed, or Mill Finish
• High Strength Low Alloy Material
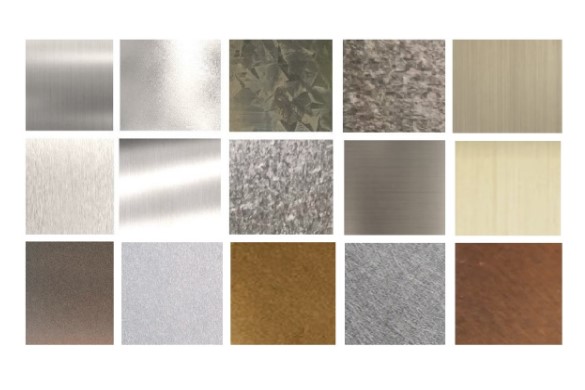
HOW IT’S MADE
Using a press brake with v-shaped die to bend metal grating into planks.
WATCH VIDEO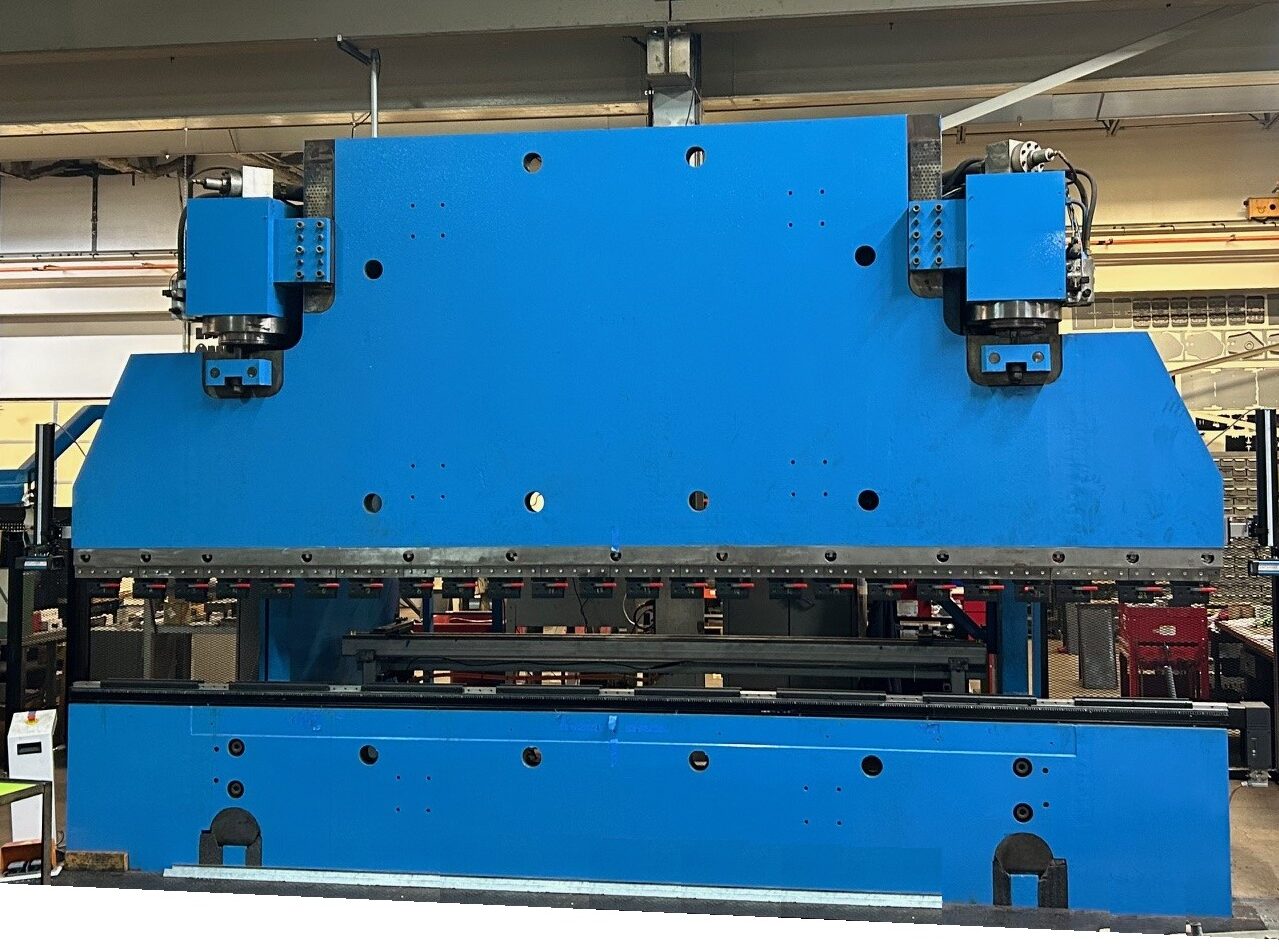
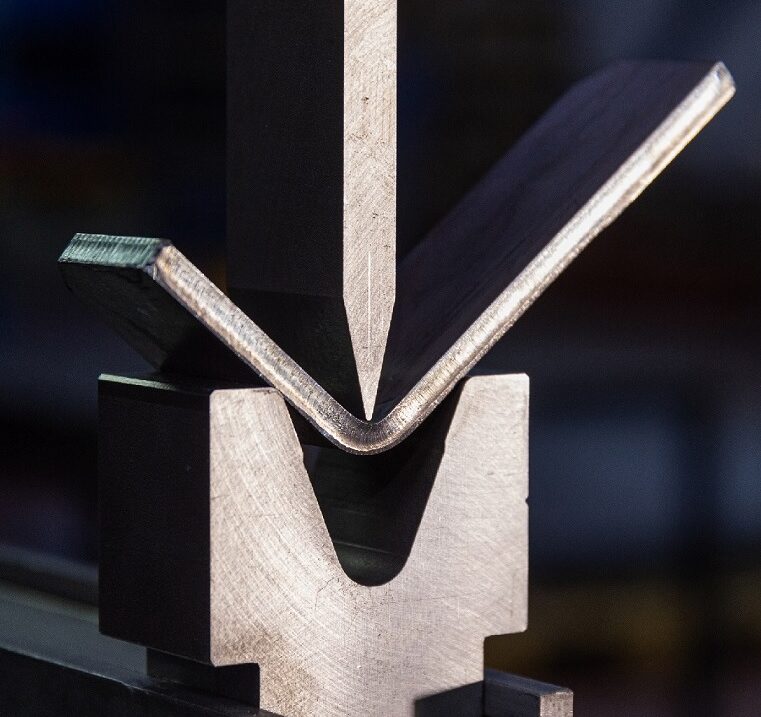
THE FKI ADVANTAGE
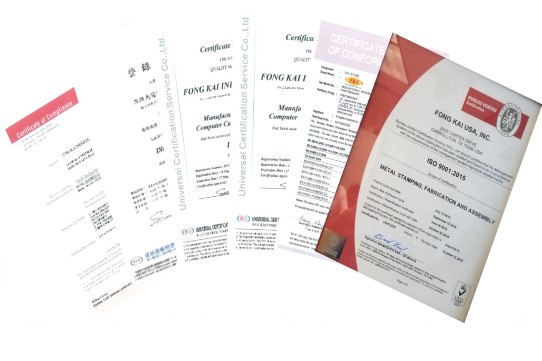
QUALITY &
CERTIFICATIONS
LEARN MORE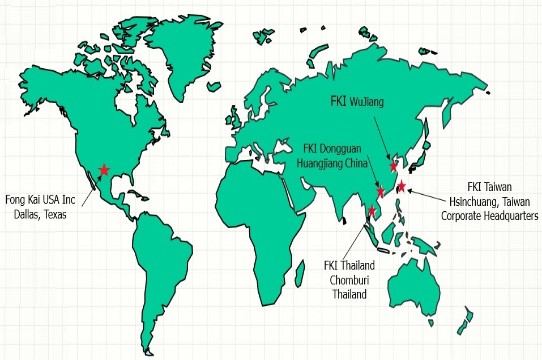
GLOBAL LOGISTICS &
PLANNING
LEARN MORE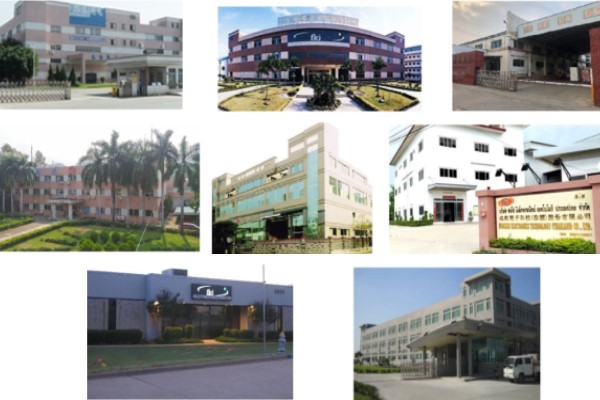