EXPLORE THE CAPABILITIES
GET STARTED TODAYA cut-to-size metal blank is moved into each die station by hand or mechanically transferred. At FKI, we can help you select the best way to meet your requirements based on quantity, tolerances, aesthetics, and size. Our professional staff and worldwide footprint are fully equipped to handle your metal stamping needs for the following industries:

IT IS ALL ABOUT COST AND QUANTITY
Mechanically moving blanks through multiple dies in a single process is excellent for larger quantities required in many industries, including automotive and consumer electronics, due to the efficiency and affordability in mass quantity. However, hand transfers are best used for small amounts or low tooling budgets. Stamping operations such as deep draw, threading, ribs, and intricate designs can be accomplished as a workpiece advances. Transfer die stamping is usually best suited for manufacturing deep-drawn or complex parts. It is also much more suitable for large parts and can reduce the need for secondary operations.
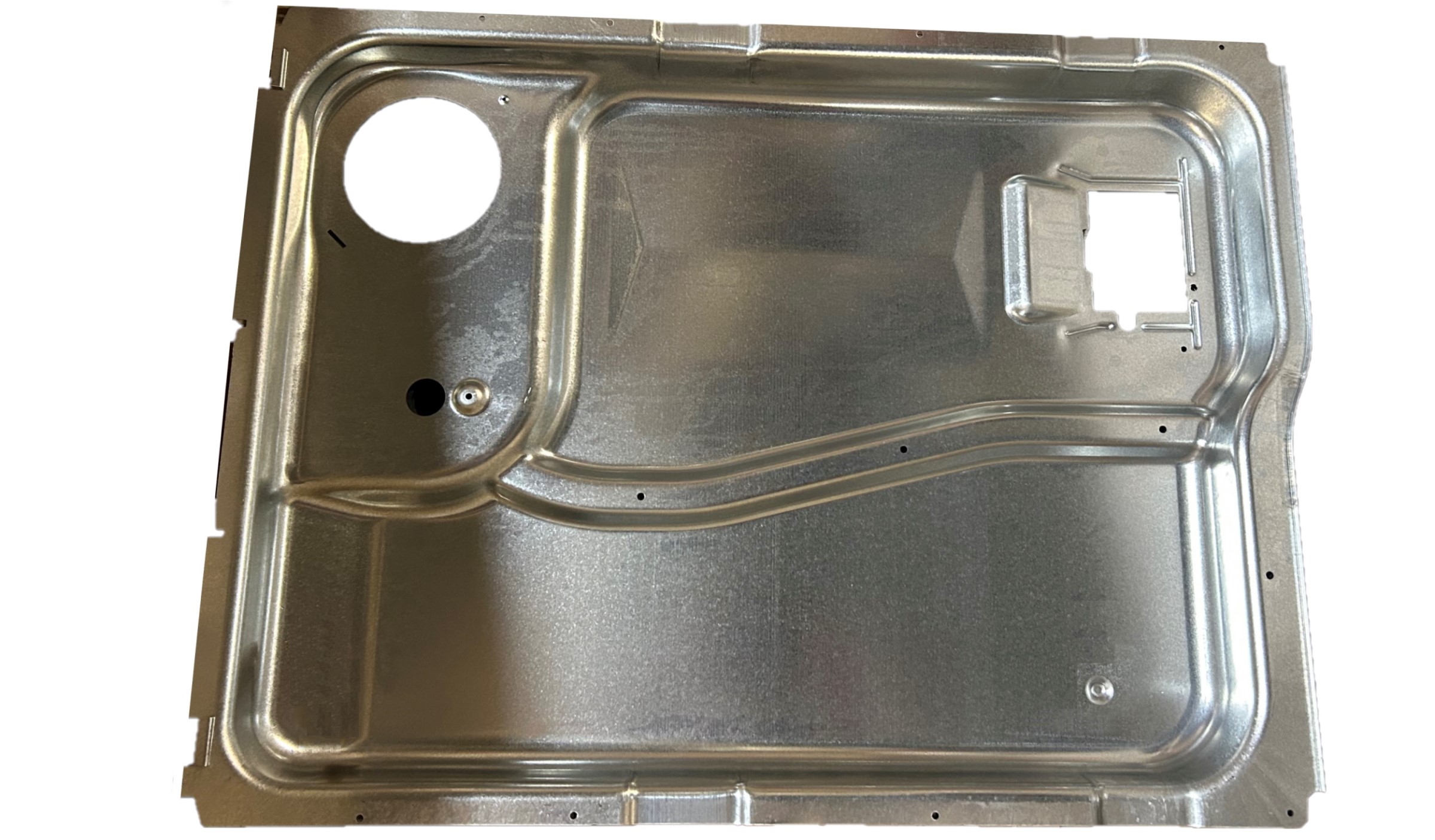
ADJUSTABLE PARTS
Transfer parts are free from the metal strip and allow for more flexibility in the part design. Typically, the flexibility makes the tools more cost-effective than progressive tooling.
VERSATILITY
The tool makes performing additional features and operations, such as threading, ribs, knurls, and deep-drawn parts, more manageable.
SPEED
Mechanical transfer systems allow parts to be handled and transferred much more quickly than hand-transferred parts.
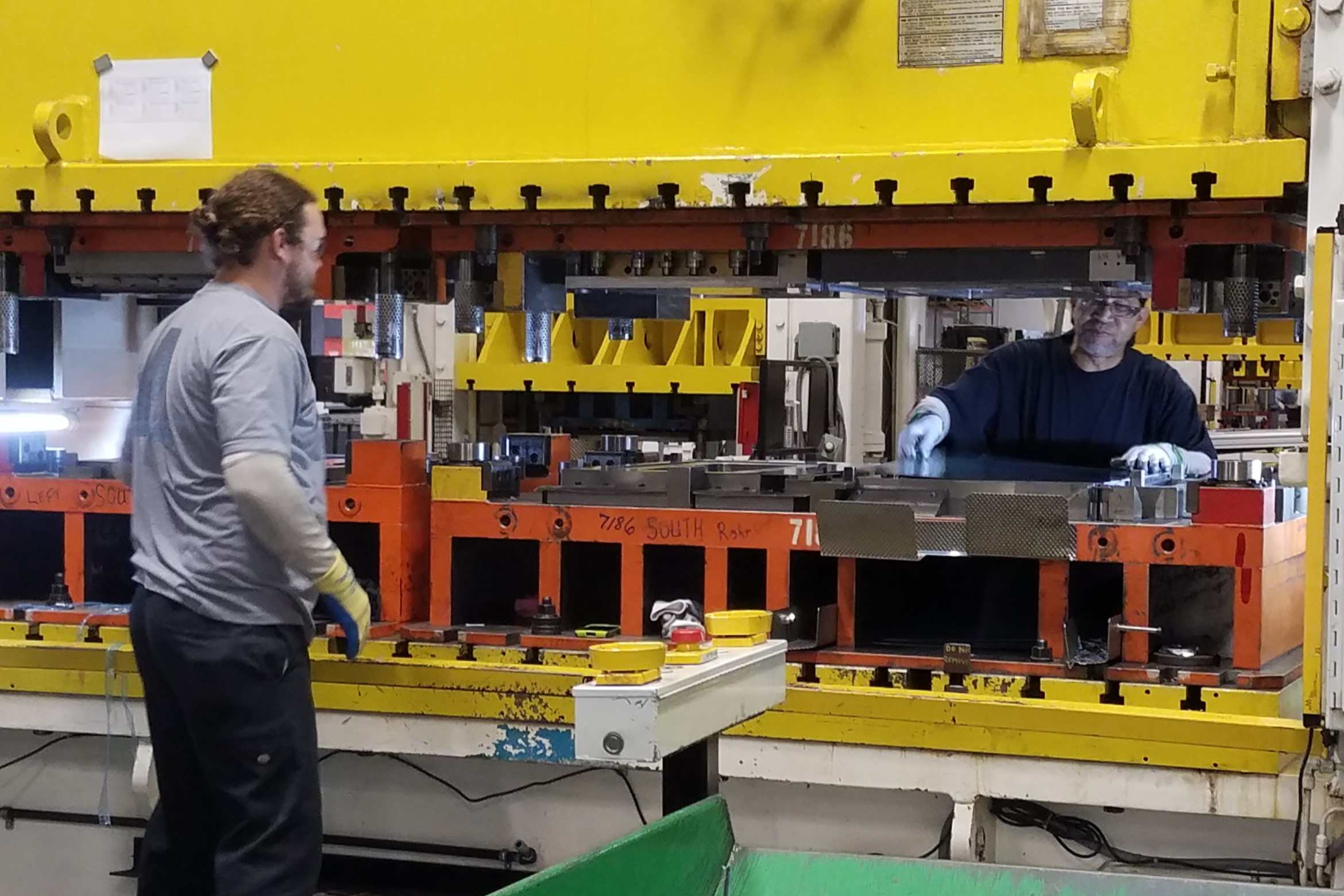
HAND TRANSFER
WATCH VIDEO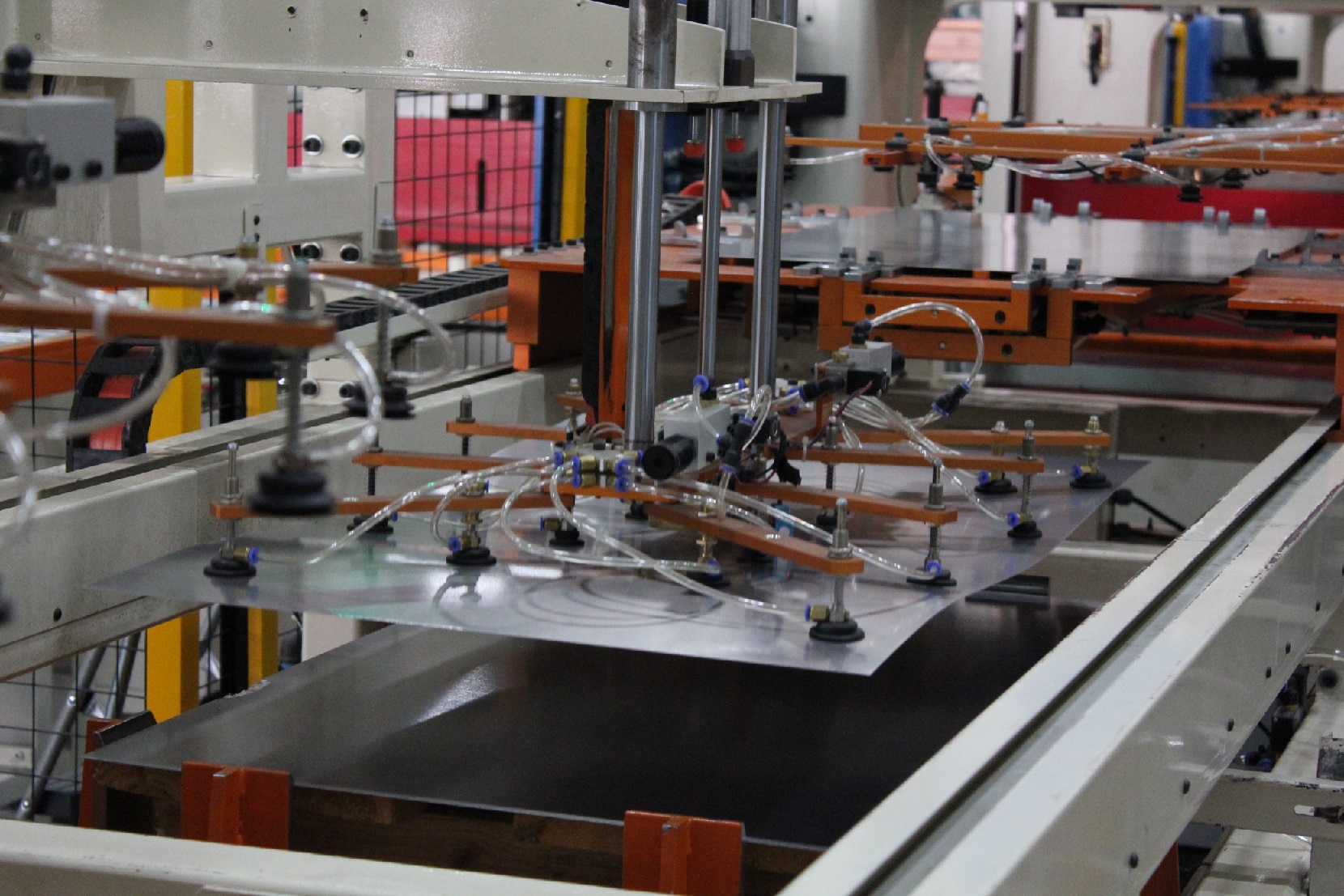
MECHANICAL TRANSFER
WATCH VIDEOSTAMPING PRESSES WORLDWIDE
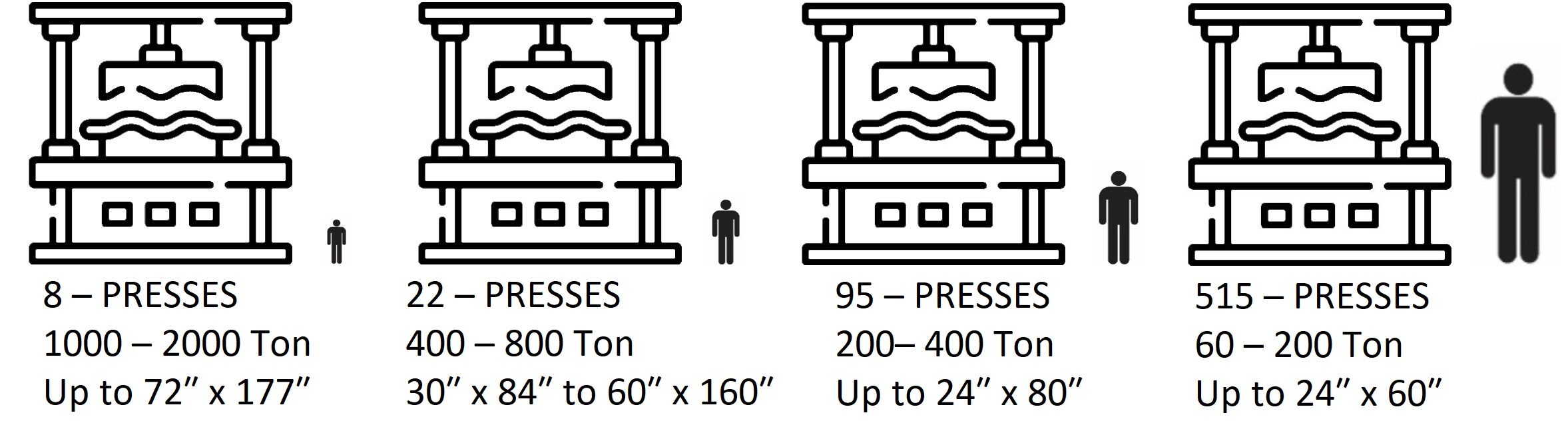
CAPABILITIES
WORLDWIDE PRODUCTION
• Over 620 metal stamping presses worldwide.
• 60 Ton up to 2000 Ton
• Presses Beds up to 72″ x 177″
• Progressive & Transfer Stamping
• Class A Cosmetic products
• Specializing in Deep Draw stamping of larger components
• Quality Capable Tooling to support tight tolerances and consistent parts
• In-House Tooling Design, Fabrication and Maintenance
• World-class manufacturing from multiple locations overseas or from our US facility
• All our stamping facilities are certified (ISO 9001) 2015
• High Volume +1,000,000 Progressive Die Stamping
• US Qualifications available to reduce overseas travel of Engineering Resources
• World-class manufacturing from multiple locations overseas or from our US facility
ADDITIONAL FEATURES INCLUDE, BUT NOT LIMITED TO:
• Fittings, Finishing, Forming, Flanges Deburring, Painting, Powder Coating, and PVD Coating
DOMESTIC OR OVERSEAS QUALIFICATIONS
With our Texas stamping and tool and die facilities, FKI will reduce engineering budgets while improving productivity. We commonly support ECN/ECR requests locally before PPAP and during product life. The strategy of approving part geometry in our overseas facilities before shipment with final buy-off and approval in Texas benefits our North American clients.
OEM PRODUCTS
Doors, Sinks, Skins, Panels, Liners, Cook Tops, Housings, Burner Bowls, Frames, Sinks, Pans, Covers, Lids, Trim, Brackets & Bases, Basins, Tanks, Trays, Wells, Chambers, Canisters, Containers, Shields, Enclosures, Reservoirs, and Basins.
SUPPORTING DEVELOPMENTS
• Complete Turnkey Project Management
• FKI can support Multiple Tool Package Developments from internal and external suppliers/customers
• Virtual Design Review
• PPAP- US Qualifications Available to Reduce Overseas Travel of Engineering Resources
• Welding, Test Fixture, and Jig Development in Accredited Certified Facilities
• Simulation Validation and Reporting
• Laser Welded Fabrication
• Build to Print
• Weldments and Assemblies
• Utilizing Fully Licensed 3D CAD software
• Zeiss CMM with Calypso
• Hexagon Laser Scanning and PC Dimensional inspection software
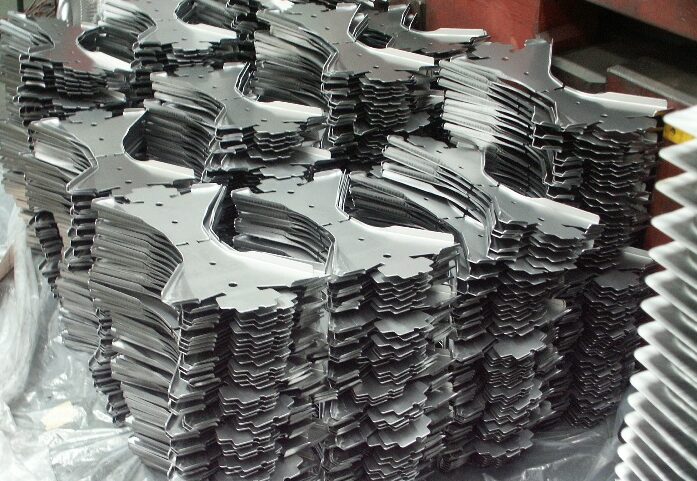
CLASS A COSMETIC
Our specialty is manufacturing high-volume cosmetic Class A decorative products that are difficult for other manufacturers. At FKI, we provide component assembly to manage the production process better and reduce manufacturing lead times. Utilizing our extensive in-house ability to develop tooling solutions domestically and leveraging our overseas partners, we can provide greater flexibility to our clients without sacrificing costs or time to the market.
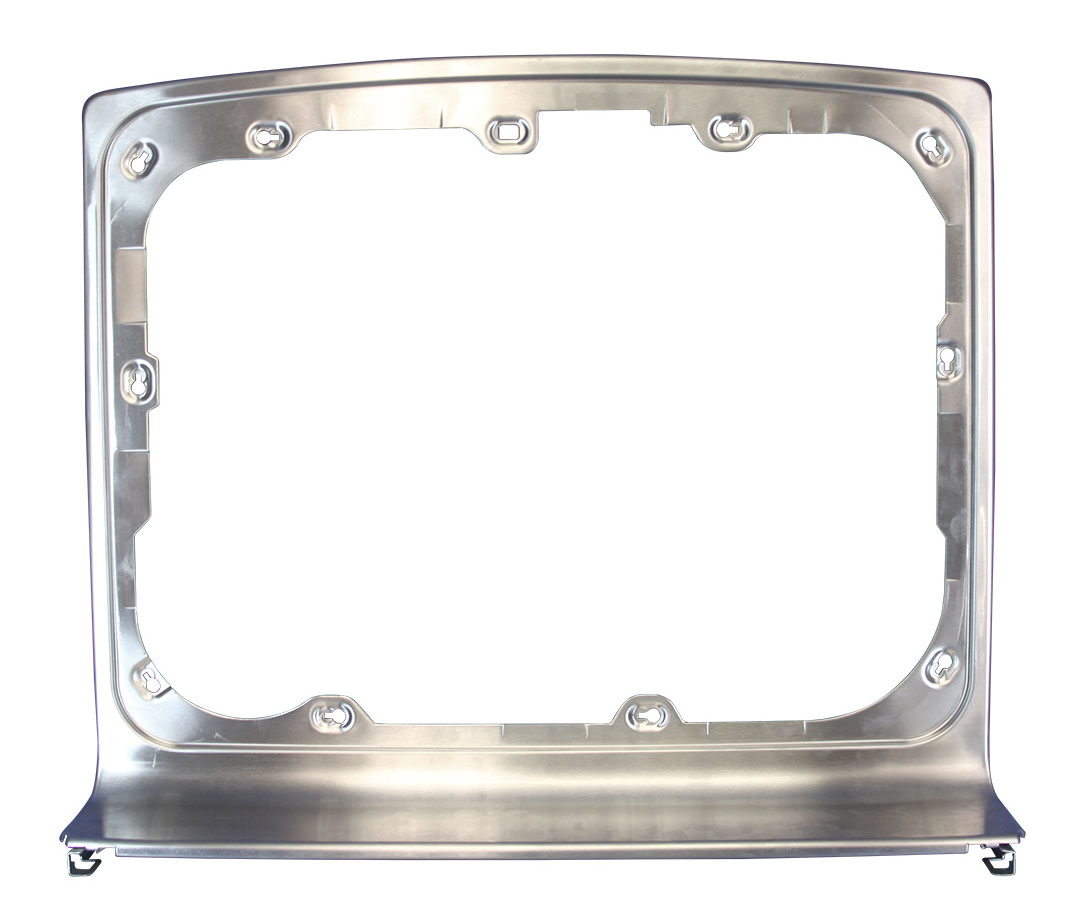
THICK, THIN, BRIGHT, SATIN & MILL FINISH
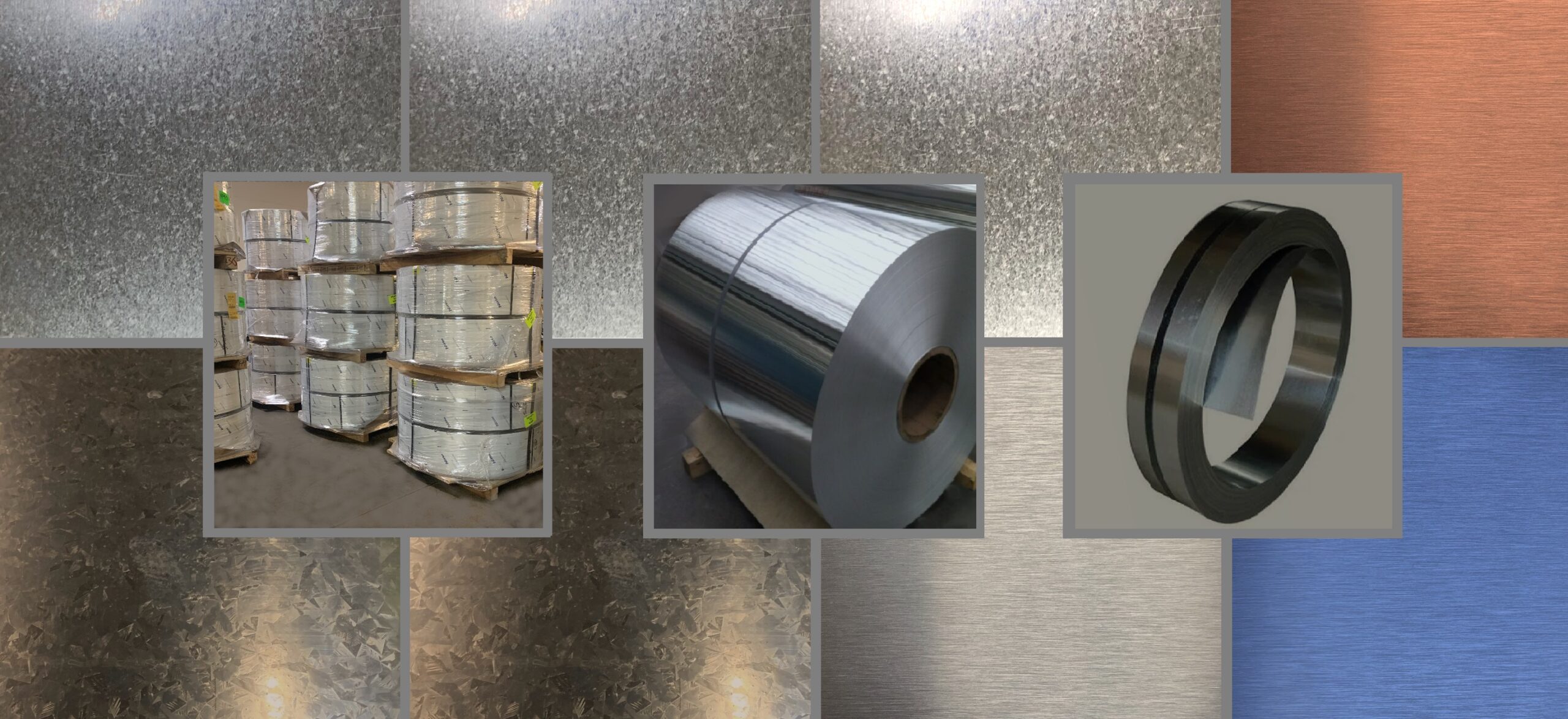
FKI can manufacture and develop simple to complex products using an assortment of metals ranging from .012” to .500” in thickness.
MATERIALS
• Stainless Steel
• Aluminum
• Cold Rolled Steel
• Pre-coated Steel & Aluminum
• Electro-Galvanized
• Aluminized Steel
• Engineered Steels
• Bright, Brushed, or Mill Finish
• High Strength Low Alloy Material
DESIGNING A METAL STAMPED PART
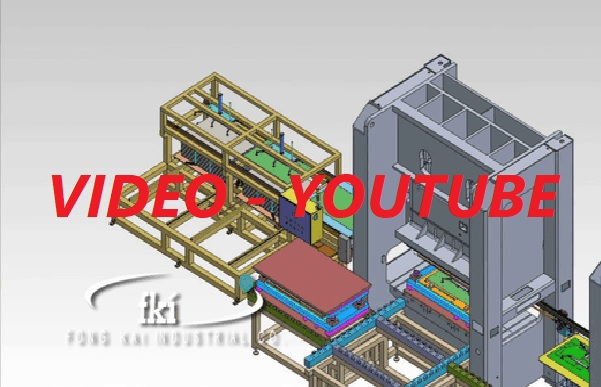
Automated line we designed, built, and installed for major appliance customer
Several key factors must be considered when designing a stamped metal component, including metal selection, durability, die design, part size, and the ability to mass produce effectively. Our Engineers help you create the best possible solution for your stamping needs and can suggest working with progressive tooling or hand transfer tools, depending on your requirements.
Watch VideoHOW IT’S MADE
A great example of combining multiple processes and hand transfers to make an appliance assembly.
THE PROCESS
• Metal is cut to a specific blank size for the duct cover and housing.
• The duct cover is placed in a stamping tool with five stations and transferred by hand from each station.
• The duct housing is placed another stamping tool with five stations and transferred by hand from each station.
• In a separate operation on another press, the (2) components are joined together.
• Throughout the process, parts are inspected for quality and packaged for the customer.
Note: In an ideal world, you would want to automate this entire process and possibly mechanically transfer parts to decrease the number of touches. However, this is ideally suited for hand transfer due to a combination of smaller quantities, many operations, and the high tooling cost.
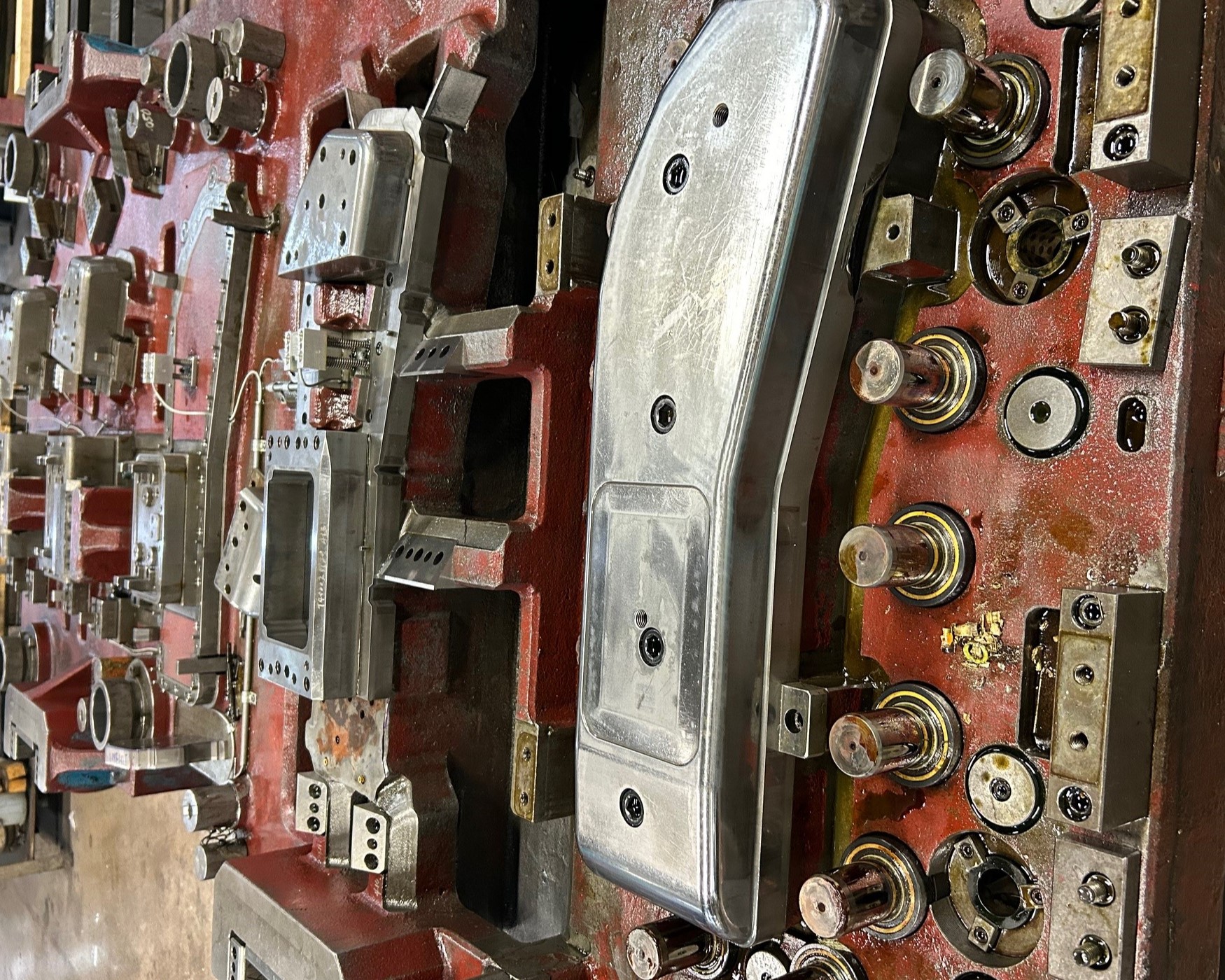
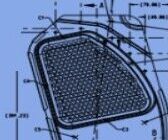
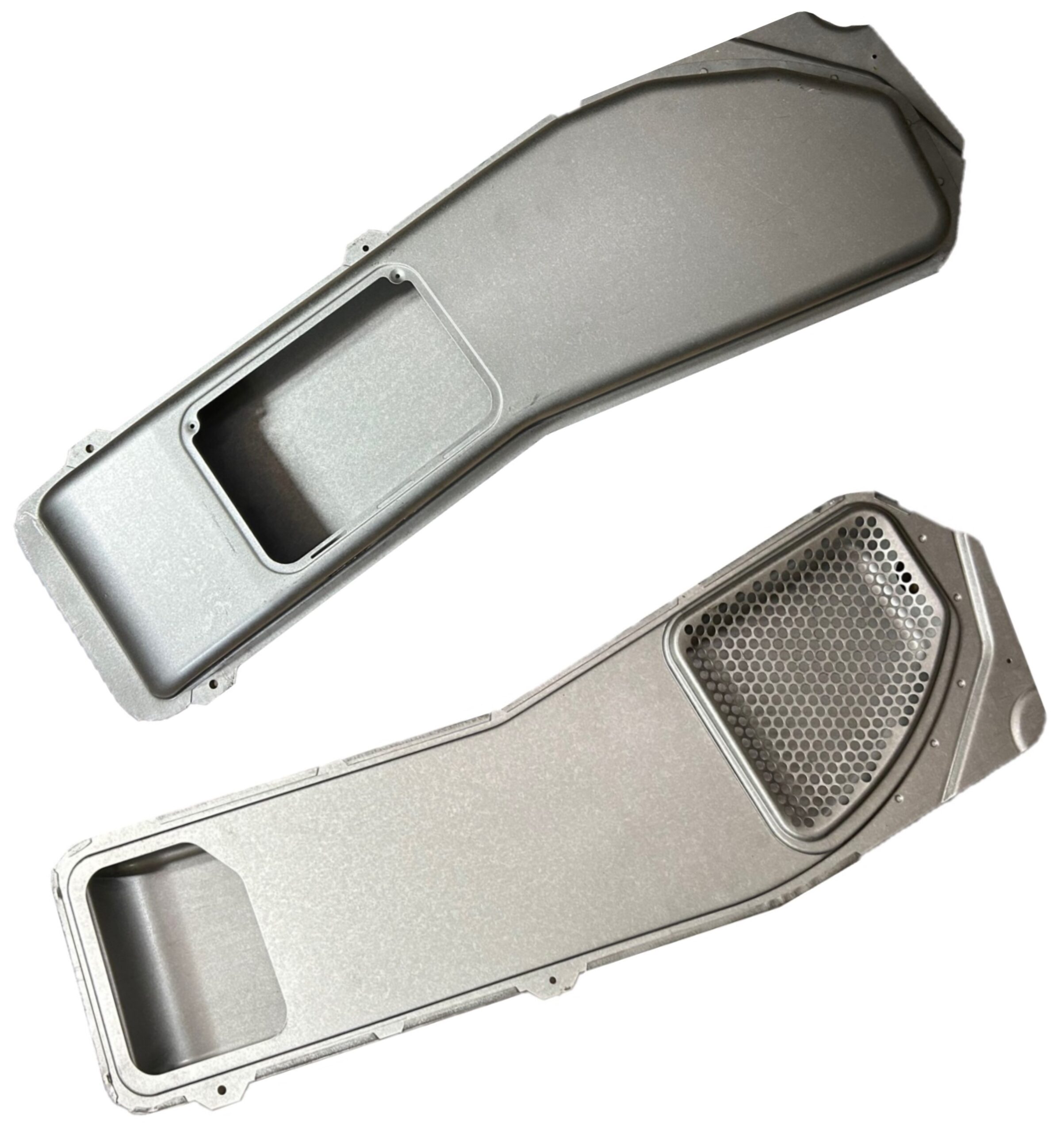
Ready to work with Fong Kai on your next project?
GET STARTED TODAYTHE FKI ADVANTAGE
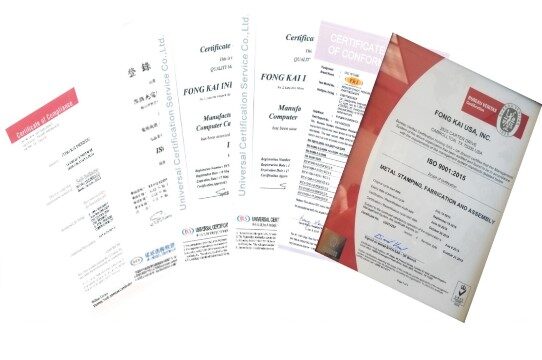
QUALITY &
CERTIFICATIONS
LEARN MORE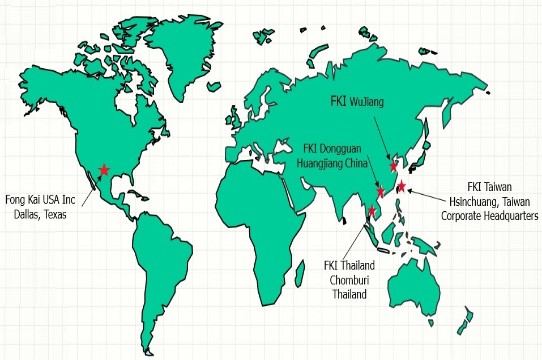
GLOBAL LOGISTICS &
PLANNING
LEARN MORE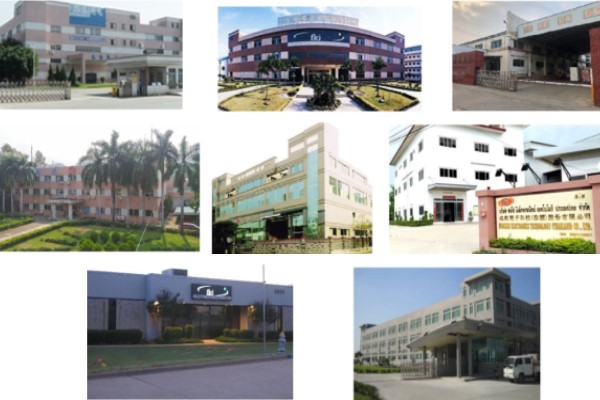